 |
 |
 |
 |
 |
 |
 |
 |
 |
 |
 |
|
|
 |
|
|
|
|
|
|
|
|
To compete in the global market for durable goods, North American manufacturers need to exploit any cost advantage they can find. They seek advantage in new labor-saving production machinery, scheduling and planning software, and team-based, incentive-driven employee management.
Advantages in material costs are harder to come by. If you make earth moving machinery or storage racks, you won't be switching from steel to plastic. But manufacturers who switch from the basic hot rolled black they've used for years to SCS are enjoying impressive, sustained cost advantages.
|
|
|
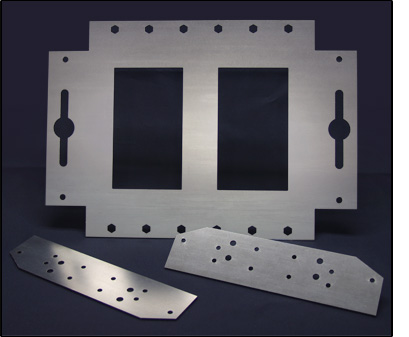 |
In the following profiles of SCS cost advantage, we are respecting the manufacturer's wish that their name not be divulged. The reason for anonymity is obvious – they don't want their competitors to learn about and duplicate their SCS advantage.
However, Manchester Tank, a leading maker of custom pressure tanks for propane, refrigerants and chemicals was willing to share some preliminary results. Steel Summit supplies Manchester with SCS sheets to replace hot rolled black and capture the SCS laser speed advantage on lasers Manchester will soon install. But before they even lasered the first sheet, they found SCS' cleanliness and complete absence of rust has allowed them to simplify their paint prep and run a cleaner shop.
|
 |
These conveyor system parts were laser cut from SCS sheets. The
manufacturer achieved a cutting speed of 175 inches/minute versus
top speeds of 155 for CRS and 120 for hot rolled black . |
SCS cleanliness is really paying off
for a tube producer in the Southeast.
They supply a manufacturer of hand |
|
rails and safety rails with tubing made |
from hot rolled black. That customer always had to shot blast the tubes to remove rust and clean them up for painting. Since switching to SCS, the customer has stopped blasting altogether, commenting that the ultra-clean SCS tubes look like they're made from cold rolled. That has helped the tube producer secure a larger share of the orders issued by this key manufacturer of railings.
|
Speaking of shot blasting . . . a heavy equipment OEM has switched their orders of hot rolled black over to SCS because of the benefits they saw from an extensive SCS trial. In fact, they have yet to determine just how extensive those benefits really are. For example, after the switch to SCS they started to increase cutting speed of their plasma tables on 0.250" SCS sheets. They quickly reached a 20% speed improvement and found they could go no farther. Why? The plasma tables had a software "governor" to limit top speed, and with SCS they had reached the limit – something the supplier of the plasma tables never expected. Once the plasma table software is reprogrammed to raise this limit, they expect to achieve cutting speed improvements of 30% or more, with no loss of cut quality.
Welding is where substantial cost savings have been captured with SCS - especially in reduction of weld rejects. Their products incorporate panels which are long – too long to be supplied as single sheets – so two sheets have to be seam welded together into a panel. The Fab Shop Manager said it was common to wirebrush the sheet edges in order to get a clean base for a good seam weld, but SCS has completely eliminated this step. SCS has also completely eliminated "undercut" as a weld defect and decreased the repair rate on seam welds by 35%. Farther down the production line, mig welding is a pervasive part of the products' assembly. The QA Manager responsible for this area has observed a large reduction in weld porosity with SCS, and an 85% reduction in the need to wirebrush edges prior to welding.
|
And what about that shot blasting? It has always been necessary for cleaning up these large fabrications after all that welding and for getting the material ready to paint. The switch to SCS has not eliminated this step, but the blasting superintendent reports that with SCS the process is faster and uses less abrasive grit. He also points out how the products made from SCS emerge with a smoother, more consistent finish. "Anybody can see it. Our customers can tell it's there," he explained.
That's exactly why SCS is such a formidable competitive weapon for manufacturers. Not only does it lower the cost to manufacture, but it provides the end-use customer with an all-around better, more consistent product.
|
|
 |
 |
 |
 |
|
|
|
|
|
|
|
 |